3 Warehousing Challenges Slowing Down Your Distribution
Posted on June 16, 2022 in 2022
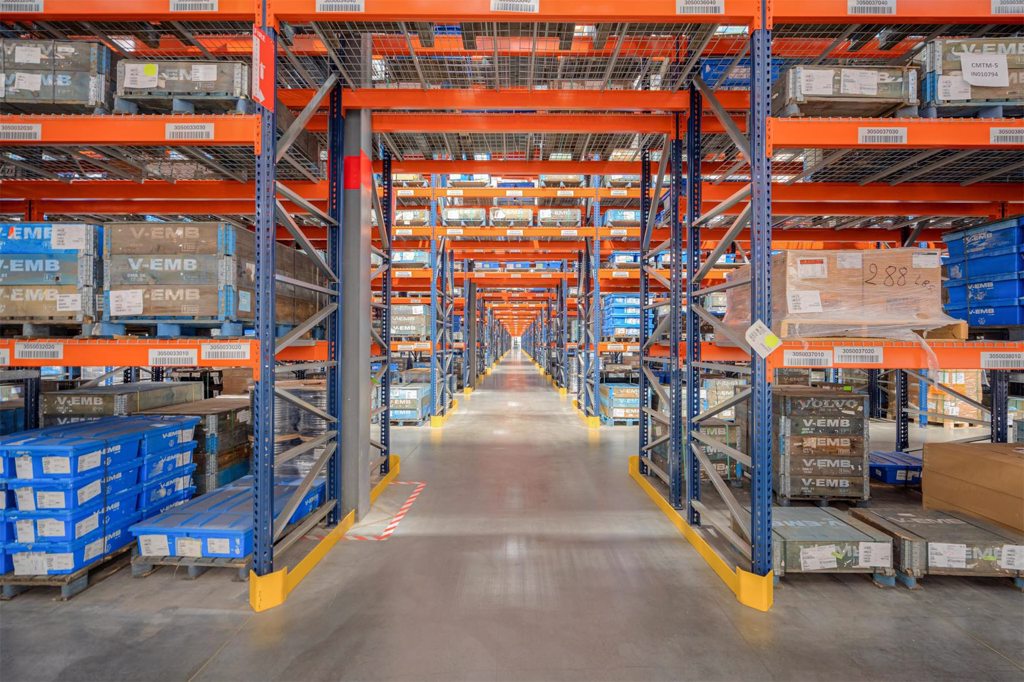
The average consumer doesn’t think about how warehouse capacity affects their ability to purchase the products they use every single day. For decades, the warehousing, distribution and logistics industry has worked tirelessly behind the scenes to ensure that the products people need simply appear on store shelves or doorsteps across America.
But recent global events have put a spotlight on major flaws in the just-in-time supply chain infrastructure. Unless you slept through the past few years, then you know that businesses everywhere have been battling significant supply chain issues, right?
What you might not know is that recent pandemic-driven activity has only accounted for the latest surge in a decade-long period of unprecedented growth across the U.S. warehousing and distribution industry.
As warehouse capacity demand has increased, it has highlighted three glaring infrastructure challenges that are already having a big impact on businesses nationwide.
1. Low Inventory – Nationwide warehouse vacancy rates hit a 27-year low in the first quarter of 2022. For businesses looking to increase capacity to meet demand, it’s a tricky problem. In coastal metropolitan areas with easy port access, warehouse real estate is essentially sold out. In many markets, if you can even find unused warehouse space, you’re probably going to pay a steep premium. And, of course, that means your distribution costs rise and take a bite out of your bottom line. Not good for business.
2. Aging Infrastructure – Back in March, the real estate services company JLL Inc. estimated that U.S. warehouse properties were 42 years old, on average. On the other hand, Newmark Group Inc., a real estate advisory firm, recently released a study that says only 14% of the country’s warehouses are less than 10 years old. That gap presents a number of challenges to modern businesses. Older warehouses tend to have lower ceilings, reduced trailer space, fewer dock doors, aging floor slabs, outdated sprinkler systems, inadequate electrical supply … the list goes on. For modern operations looking to expand, this aging infrastructure is simply not viable, leaving many companies with no choice but to build new.
3. Cost to Build – Remember those global supply chain issues we talked about a few paragraphs ago? The ones that drove the cost of lumber and new home construction through the roof? Well, the same material shortages and subsequent price increases that have plagued the residential building market are at play in the industrial warehouse construction space as well. Last August, the cost of steel tripled the previous decade’s average and it hasn’t exactly eased up since. In fact, the price of steel recently eclipsed it’s 2008 high of $1,800 per ton. But cost is only part of the equation. Delivery times have increased from an average of 12-month turnarounds to 16 or even 18 months. And steel isn’t the only construction commodity on the rise. Concrete, roofing material, and other essential elements of warehouse construction have spiked. By some estimations, the cost of materials alone has eclipsed the entire start-to-finish construction cost of just a few years ago.
Despite these challenges, there is good reason to believe that the future of warehousing is still bright. Here at Patton, we currently manage more than 3,000,0000 sq. ft. of warehousing space, with state-of-the-art AIB audited food grade facilities available. And we’re always growing and adapting to meet the needs of the growing businesses we serve.
From our cutting-edge warehouse management system to our team of dedicated pros building on more than 175 years of supply chain problem solving experience, we’ve got the capacity and the capability to help you handle all your warehousing challenges.
See how these businesses benefit from our warehousing solutions.